1 Design Of Heat Exchanger Tube In Ansys Download Scientific Diagram
Ansys Heat Exchanger Pdf Extrusion Geometry In this paper, the shell and tube heat exchanger is analyzed with ansys fluid flow (fluent), where the shell contains of tubes inside it. the hot water flows through the tubes and. Shell and tube heat exchanger is built of round tubes mounted in a cylindrical shell with the tube axis parallel to that of the shell. in shell and tube, one fluid flow inside the tube, the other flow across and along the tubes.
Design And Analysis Of Shell And Tube Heat Exchanger Pdf Heat The hot fluid (steam) velocity is 0.001 m s and the temperature is each tube is different (tube 1 – 400k, tube 2 – 410 k, tube 3 – 420 k, tube 4 – 430 k, tube 5 – 440 k, tube 6 – 450 k). the steam passes through 6 steel tubes. table of contents 1. The objective of this simulation example is to analyze the heat transfer in a shell and tube heat exchanger configuration. the system would have hot oil flowing through the shell and cold water passing through the tubes. setup. download the mesh file required for setting up the simulation and associated case & data files here. follow the. Ansys fluent provides two distinct methods of modeling a heat exchanger: the dual cell model and the macro model. these models can be used to compute the auxiliary fluid inlet temperature for a fixed heat rejection or the total heat rejection for a fixed auxiliary fluid inlet temperature. This tutorial video shows the basic of how to conduct sthe analysis using ansys fluent. poly hexcore mesh was used in this tutorial. the step file of the sth.
Lecture Mechanical Design Of Heat Exchanger Download Free Pdf Pipe Ansys fluent provides two distinct methods of modeling a heat exchanger: the dual cell model and the macro model. these models can be used to compute the auxiliary fluid inlet temperature for a fixed heat rejection or the total heat rejection for a fixed auxiliary fluid inlet temperature. This tutorial video shows the basic of how to conduct sthe analysis using ansys fluent. poly hexcore mesh was used in this tutorial. the step file of the sth. In this lesson we talked about the analysis of heat exchangers and discussed how we can perform design and performance calculations. lastly, we looked at the procedure used in heat transfer design and performance calculations. Tubular heat exchanger design theory is that the fluid is distributed uniformly at the inlet of the exchanger on each fluid side throughout the core. however, in practice, flow maldistribution is more common and significantly reduces the idealized heat exchanger performance. flow maldistribution can be induced by. In present study the shell and tube heat exchanger with straight tubes and double pass is under study. task is to design the heat exchanger to exchange the heat between methylene. Current paper, a shell and tube heat exchanger is design will be based on the kern’s method. the design obtained from the kern’s technique is analysed and evaluated using the cfd software which will give us a detailed view of the temperature, velocity and pressure profile. these figure 1.4 shell and tube heat exchangers. (a) one shell.
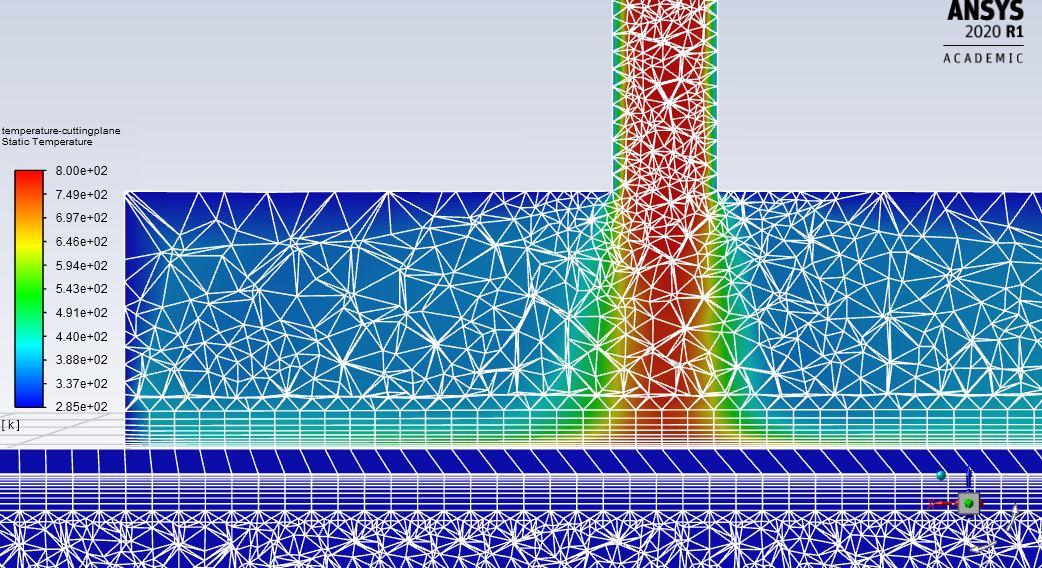
Heat Exchanger Ansys Learning Forum In this lesson we talked about the analysis of heat exchangers and discussed how we can perform design and performance calculations. lastly, we looked at the procedure used in heat transfer design and performance calculations. Tubular heat exchanger design theory is that the fluid is distributed uniformly at the inlet of the exchanger on each fluid side throughout the core. however, in practice, flow maldistribution is more common and significantly reduces the idealized heat exchanger performance. flow maldistribution can be induced by. In present study the shell and tube heat exchanger with straight tubes and double pass is under study. task is to design the heat exchanger to exchange the heat between methylene. Current paper, a shell and tube heat exchanger is design will be based on the kern’s method. the design obtained from the kern’s technique is analysed and evaluated using the cfd software which will give us a detailed view of the temperature, velocity and pressure profile. these figure 1.4 shell and tube heat exchangers. (a) one shell.
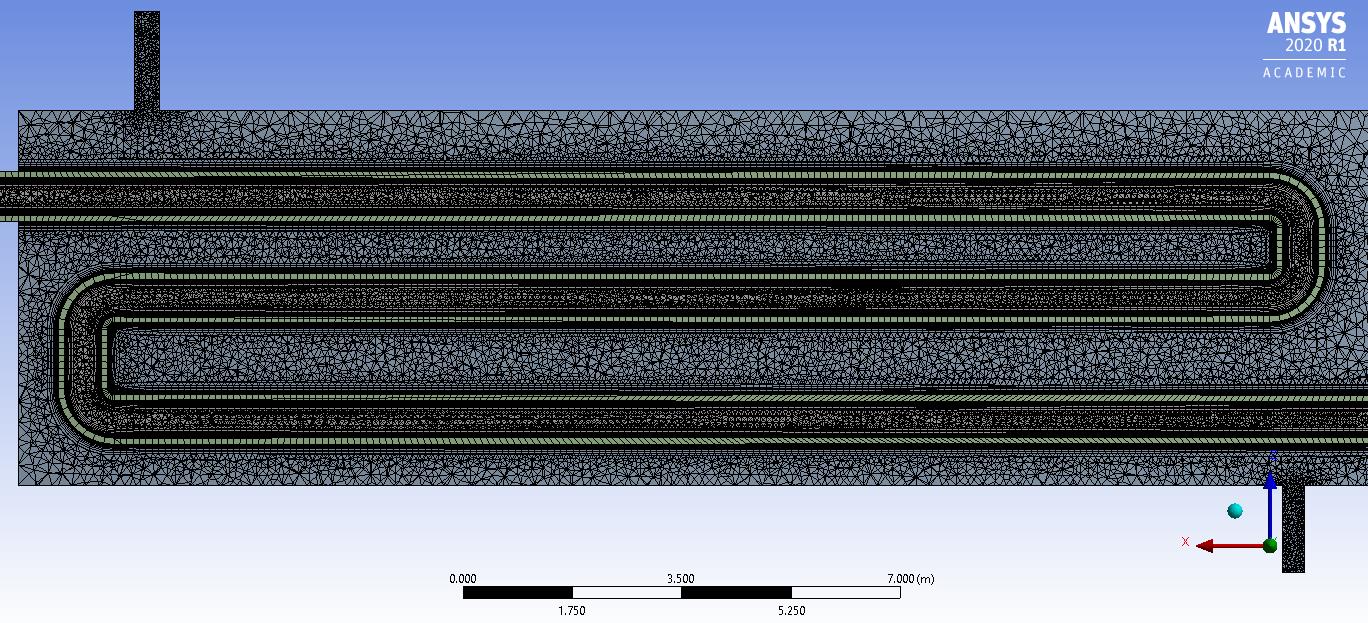
Heat Exchanger Ansys Learning Forum In present study the shell and tube heat exchanger with straight tubes and double pass is under study. task is to design the heat exchanger to exchange the heat between methylene. Current paper, a shell and tube heat exchanger is design will be based on the kern’s method. the design obtained from the kern’s technique is analysed and evaluated using the cfd software which will give us a detailed view of the temperature, velocity and pressure profile. these figure 1.4 shell and tube heat exchangers. (a) one shell.

1 Design Of Heat Exchanger Tube In Ansys Download Scientific Diagram
Comments are closed.