Design And Meshing Of Helical Pipe Heat Exchanger In Ansys Workbench Fluent Part 1

Ansys Workbench Cfx Heat Exchanger 3d Cad Model Library 47 Off Hello, my dear subscribers of contour analysis channel. thank you for watching the analysis video on my channel, i hope you will share and lear. There are different meshing methods in ansys, including tetra meshing, hexa meshing, quad tri meshing, sweep meshing, multi zone meshing etc. the choice of meshing method depends on the type of analysis and the characteristics of the geometry. here we use the multi zone meshing method.

Ansys Workbench Cfx Heat Exchanger 3d Cad Model Library 47 Off This video shows how to model meshing in a shell and tube heat exchanger using ansys meshing. for any questions support, join ansys student community: https:. 1. selecting a heat exchanger that will achieve a specified temperature change in a fluid stream of known mass flow rate 2. predicting the outlet temperatures of the hot and cold fluid streams in a specified heat exchanger •in this lesson we will discuss two methods used in the analysis of heat exchangers:. Information on how to deal with thin regions, quad tet transition elements (pyramid and non conformal meshing), and creation of a heat exchanger zone are also described. detailed descriptions of meshing techniques such as prism meshing, tetrahedral and hexcore meshing options, and so on are described in subsequent chapters. In this video. to describe the geometry and meshing of a heat exchanger having spiral type pipes using a geometry design modeler in fluent software. in the next video, i will show the.
Lecture Mechanical Design Of Heat Exchanger Download Free Pdf Pipe Information on how to deal with thin regions, quad tet transition elements (pyramid and non conformal meshing), and creation of a heat exchanger zone are also described. detailed descriptions of meshing techniques such as prism meshing, tetrahedral and hexcore meshing options, and so on are described in subsequent chapters. In this video. to describe the geometry and meshing of a heat exchanger having spiral type pipes using a geometry design modeler in fluent software. in the next video, i will show the. The process in solving simulation consists of modelling and meshing the basic geometry of shell and tube heat exchanger using cfd package ansys 15.0. the objective of the project is to design the shell and tube heat exchanger with different baffles and study the pressure drop inside the shell using fluent software. In this study, an attempt has been made to analyze the effect of counter flow on the effectiveness from a helical tube. the heat exchanger was modeled in catia, grid was generated i.e. meshed in ansys workbench and the temperature contours, velocity vectors was calculated and plotted using fluent. This tutorial illustrates using ansys fluent fluid flow systems in ansys workbench to set up and solve a three dimensional turbulent fluid flow and heat transfer problem in a mixing elbow. it is designed to introduce you to the ansys workbench tool set using a simple geometry. I have a double pipe heat exchanger in which the inner pipe has a helical outer wall as illustrated on the picture: i attempting to add mesh to the pipe but it took a too long time (approximately 8 hours) and the mesh never appear to me? how i can make a minimum number of mesh with maximum skewness not exceeds 0.76?.

Adding Mesh To Helical Double Pipe Heat Exchanger The process in solving simulation consists of modelling and meshing the basic geometry of shell and tube heat exchanger using cfd package ansys 15.0. the objective of the project is to design the shell and tube heat exchanger with different baffles and study the pressure drop inside the shell using fluent software. In this study, an attempt has been made to analyze the effect of counter flow on the effectiveness from a helical tube. the heat exchanger was modeled in catia, grid was generated i.e. meshed in ansys workbench and the temperature contours, velocity vectors was calculated and plotted using fluent. This tutorial illustrates using ansys fluent fluid flow systems in ansys workbench to set up and solve a three dimensional turbulent fluid flow and heat transfer problem in a mixing elbow. it is designed to introduce you to the ansys workbench tool set using a simple geometry. I have a double pipe heat exchanger in which the inner pipe has a helical outer wall as illustrated on the picture: i attempting to add mesh to the pipe but it took a too long time (approximately 8 hours) and the mesh never appear to me? how i can make a minimum number of mesh with maximum skewness not exceeds 0.76?.
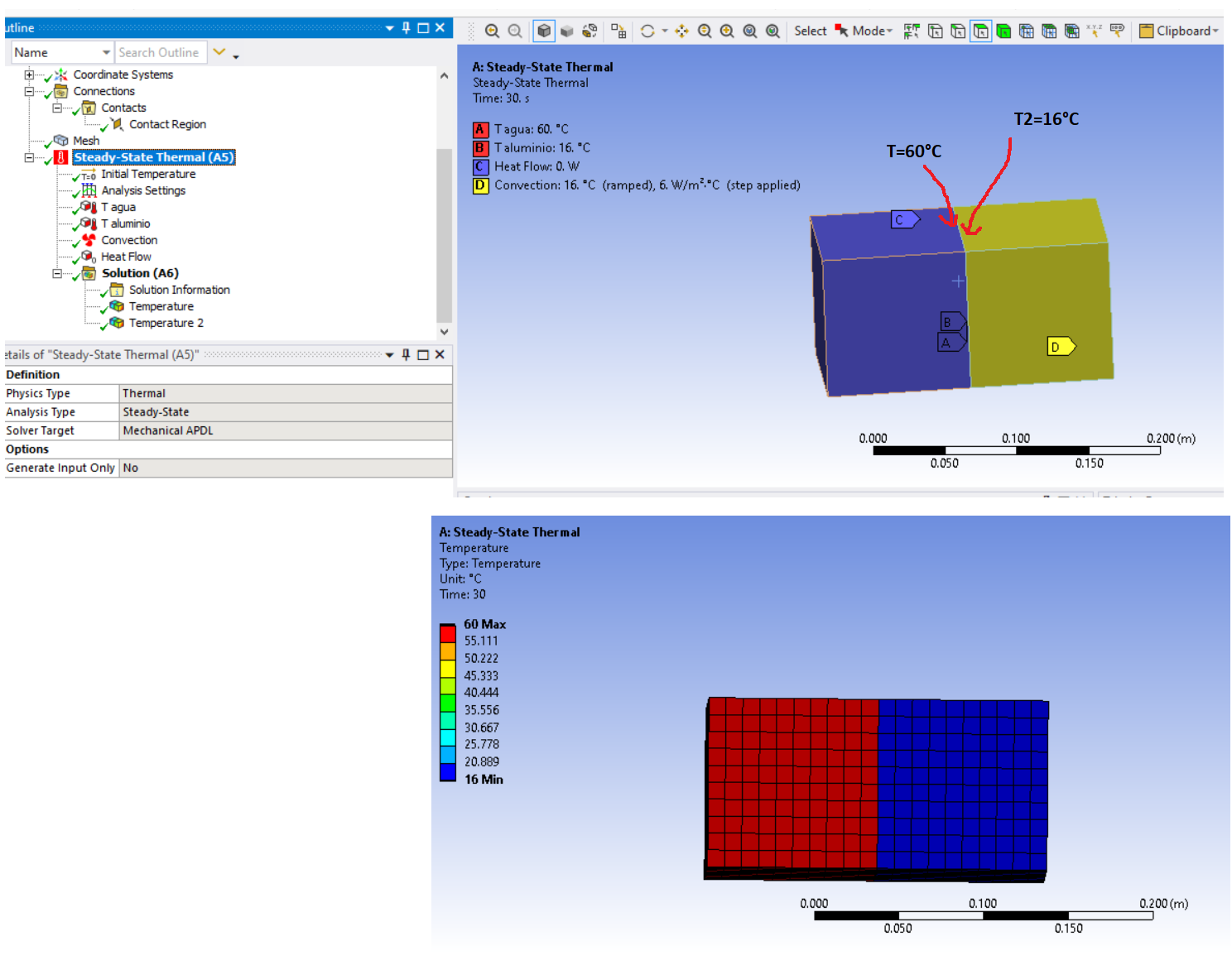
Heat Transfer Ansys Workbench Bewteen Two Objects Ansys Learning Forum This tutorial illustrates using ansys fluent fluid flow systems in ansys workbench to set up and solve a three dimensional turbulent fluid flow and heat transfer problem in a mixing elbow. it is designed to introduce you to the ansys workbench tool set using a simple geometry. I have a double pipe heat exchanger in which the inner pipe has a helical outer wall as illustrated on the picture: i attempting to add mesh to the pipe but it took a too long time (approximately 8 hours) and the mesh never appear to me? how i can make a minimum number of mesh with maximum skewness not exceeds 0.76?.
Comments are closed.