Electrical Discharge Machining Edm Copper Combined Electrodes

Edm Electrical Discharge Machining Cirtec This paper describes the application of electrodes fabricated by the am method to electrical discharge machining. almost fully dense additive manufactured copper electrode (am cu electrode) having more than 99.7% relative density was obtained by optimizing the laser scanning parameters for cu 1.3mass%cr (cu cr) alloy powder. The most important cost element of electric discharge machining (edm) is the production of tool electrode (shortly electrode). in the edm process, copper and its alloys are often used as electrode materials. the machining with edm without increasing the costs can be achieved by selecting the proper electrode with low production and material.
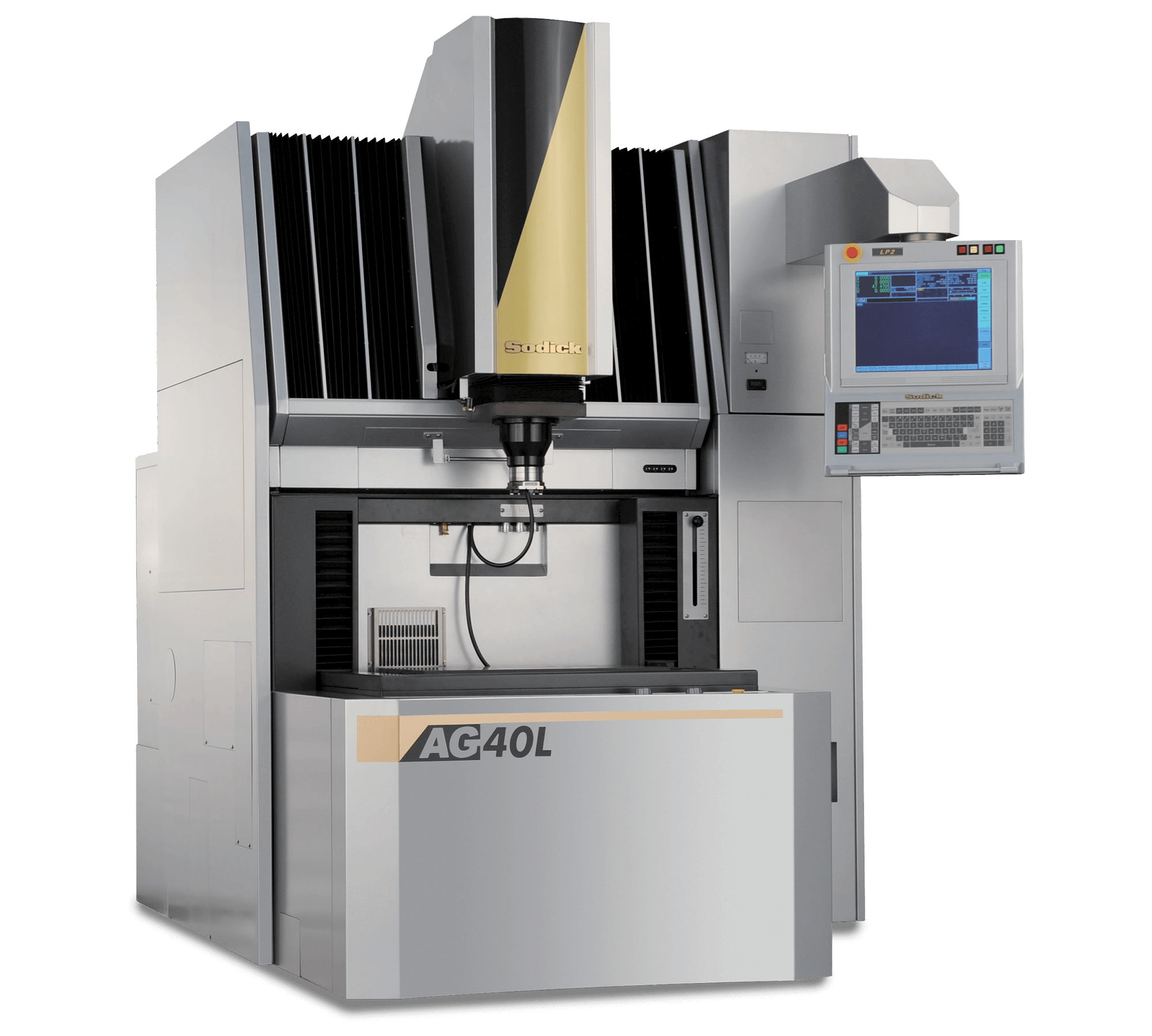
Edm Electrical Discharge Machining Cdl Creative Development In this study, the edm performance outputs, namely, mrr and rw were experimentally investigated for electrolytic copper, cucr1zr (with and without aging treatment) and cuco2be alloy electrode. Husain rizvi and sanjay agrawal (2016) studied the use of a copper tungsten electrode in electrical discharge machining. using a cnc edm machine, the association between the edm input factors and different output parameters, including surface integrity, mrr, sr, and the degree of generated residual stress, was established . Wire electrical discharge machining (edm) is a machining process that uses a slender wire, which is electrically charged, to effectively sever the workpiece. in contrast, sink electrical discharge machining (edm) utilizes specially shaped electrodes to generate cavities or distinctive characteristics inside the workpiece. 13. In our study, acrylonitrile butadiene styrene is coated with a thin layer of copper and is used as an electrode tool in powder mixed electro discharge machining (pm edm). we have employed the fused deposition modeling (fdm) method of rapid prototyping to improve the conductivity of the electrode tools for the pm edm.
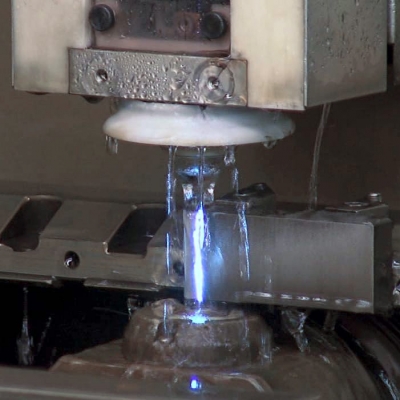
Electrical Discharge Machining Edm Services Fabrication Services Wire electrical discharge machining (edm) is a machining process that uses a slender wire, which is electrically charged, to effectively sever the workpiece. in contrast, sink electrical discharge machining (edm) utilizes specially shaped electrodes to generate cavities or distinctive characteristics inside the workpiece. 13. In our study, acrylonitrile butadiene styrene is coated with a thin layer of copper and is used as an electrode tool in powder mixed electro discharge machining (pm edm). we have employed the fused deposition modeling (fdm) method of rapid prototyping to improve the conductivity of the electrode tools for the pm edm. In the present work, a new technical approach combining equal channel angular pressing (ecap) and deep cryogenic treatment (dct) was put forward to manufacture copper electrodes for enhancing the machining characteristics of electric discharge machining (edm). The multi hole inner flushing applied in bunched electrode edm benefits to erosion products removal, and then leads to a better gap status and high process stability. although a longer finishing time is needed, the very high machining efficiency makes bunched electrode edm method has a significant advantage in rough edm process. Applying a thin coating of copper to prototyped parts by electroless metallization has provided direct method from model to tool. fused deposition modeling (fdm) process of rapid prototyping is employed to develop the electrode for electro discharge machining (edm). Electrical discharge machining (edm) is a non traditional method of precision machining that uses thermal energy and a controlled electrical spark to remove material from a workpiece. edm can also be referred to as spark machining and spark erosion. electrodes are used to generate an electrical current through non metal objects.
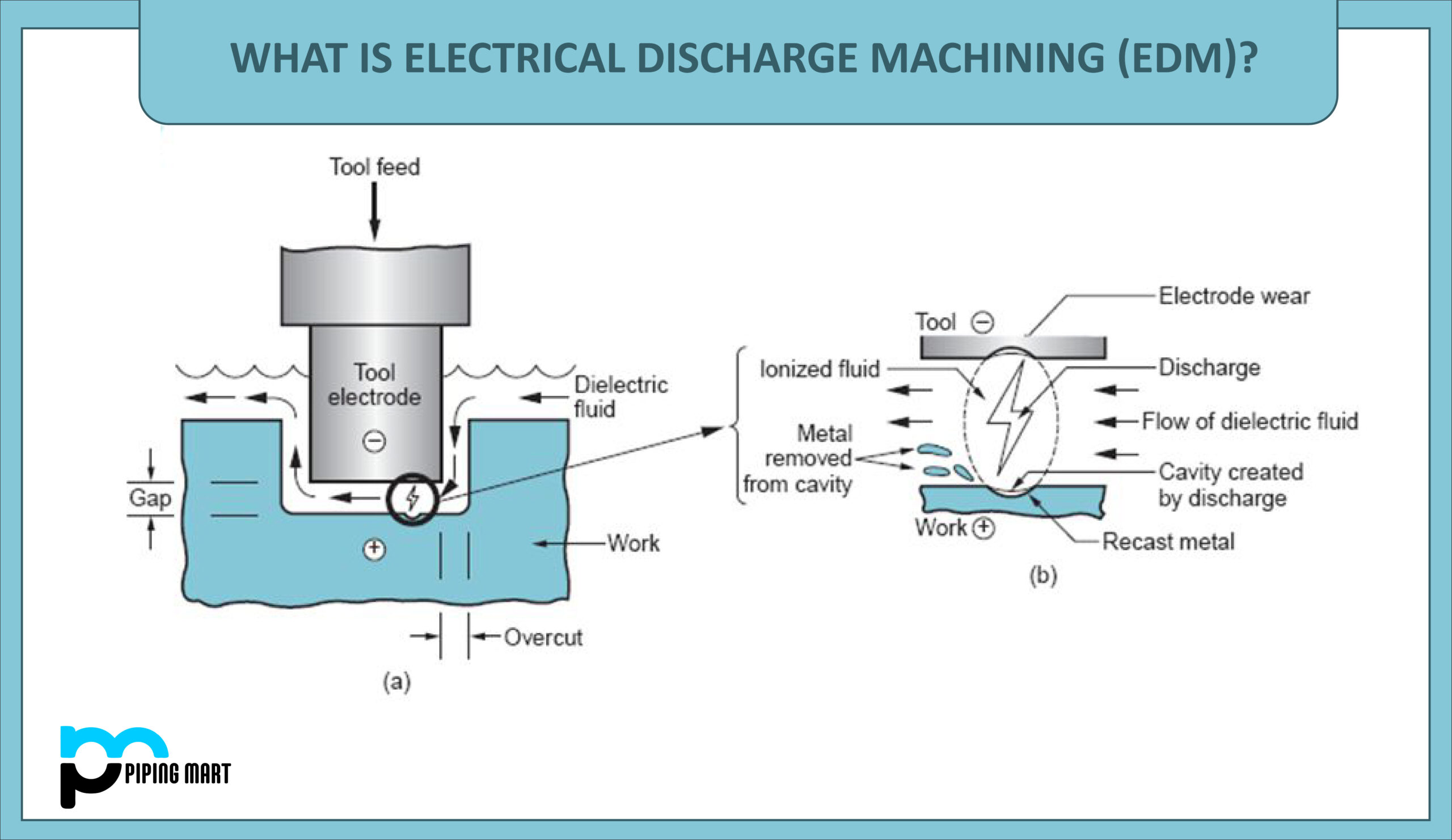
Electrical Discharge Machining Edm Everything You Need 43 Off In the present work, a new technical approach combining equal channel angular pressing (ecap) and deep cryogenic treatment (dct) was put forward to manufacture copper electrodes for enhancing the machining characteristics of electric discharge machining (edm). The multi hole inner flushing applied in bunched electrode edm benefits to erosion products removal, and then leads to a better gap status and high process stability. although a longer finishing time is needed, the very high machining efficiency makes bunched electrode edm method has a significant advantage in rough edm process. Applying a thin coating of copper to prototyped parts by electroless metallization has provided direct method from model to tool. fused deposition modeling (fdm) process of rapid prototyping is employed to develop the electrode for electro discharge machining (edm). Electrical discharge machining (edm) is a non traditional method of precision machining that uses thermal energy and a controlled electrical spark to remove material from a workpiece. edm can also be referred to as spark machining and spark erosion. electrodes are used to generate an electrical current through non metal objects.
Electro Discharge Machining Edm Submitted To Submitted By Pdf Applying a thin coating of copper to prototyped parts by electroless metallization has provided direct method from model to tool. fused deposition modeling (fdm) process of rapid prototyping is employed to develop the electrode for electro discharge machining (edm). Electrical discharge machining (edm) is a non traditional method of precision machining that uses thermal energy and a controlled electrical spark to remove material from a workpiece. edm can also be referred to as spark machining and spark erosion. electrodes are used to generate an electrical current through non metal objects.
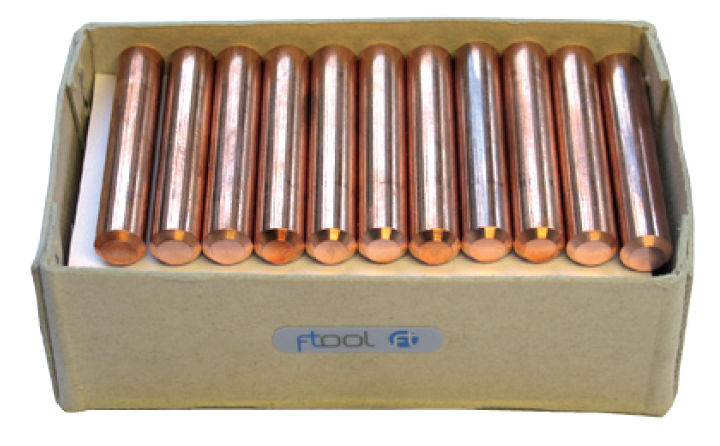
Edm Electrode Copper Process Ritm Industry
Comments are closed.