What Is Directed Energy Deposition Ded Types Pros And Cons
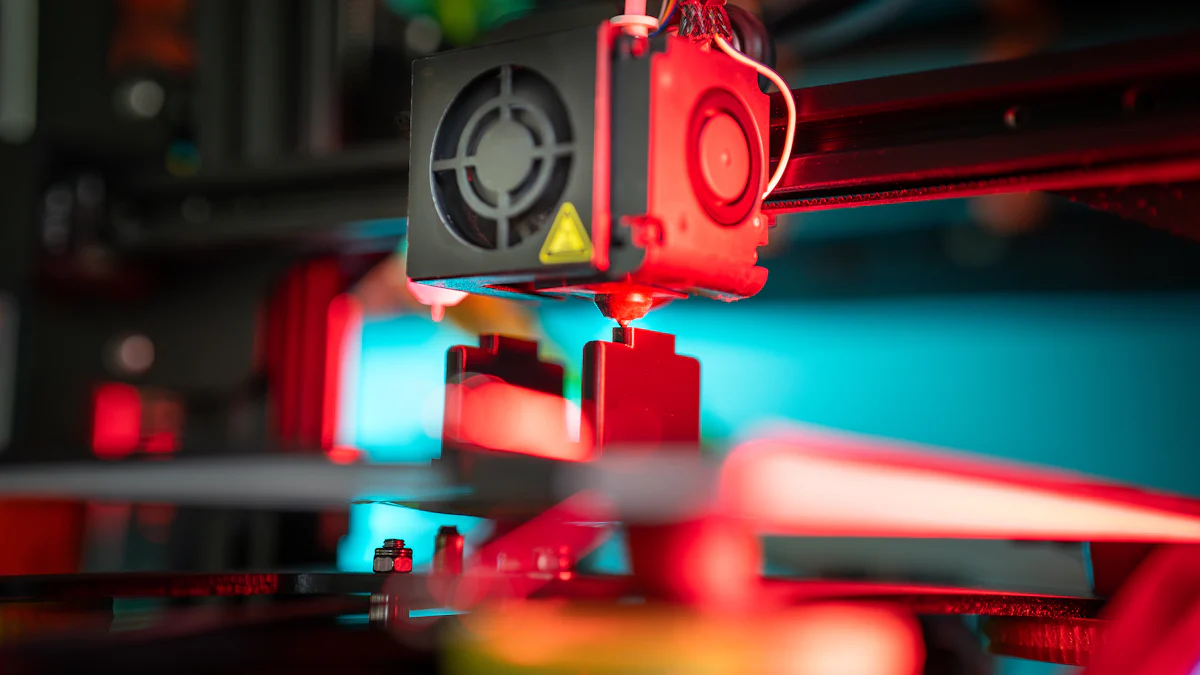
Top 3 Pros And Cons Of Directed Energy Deposition Ebm Machine Laser based directed energy deposition (ded) employs a high power laser to melt materials during deposition, allowing for exceptional precision and versatility with various metals and alloys such as titanium, steel, and inconel. Directed energy deposition (ded) offers significant advantages, such as high material efficiency, versatility, and precision. however, it also presents challenges, including high initial costs and complexity in process control.
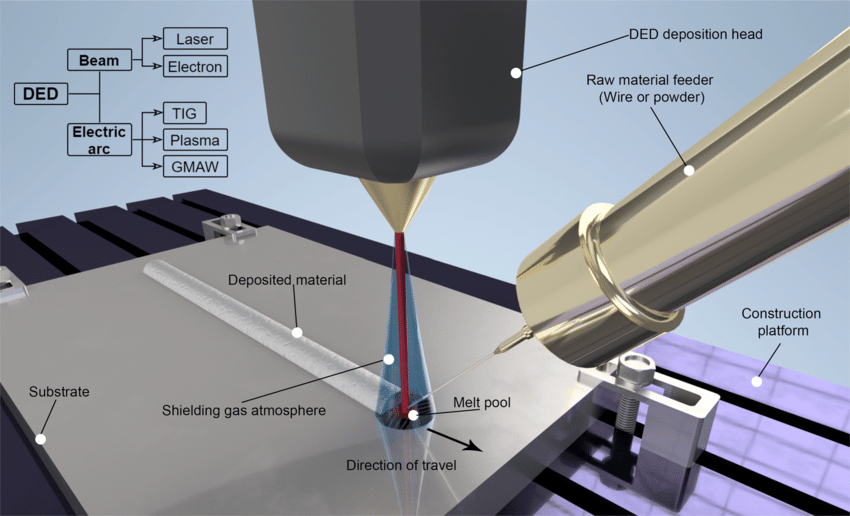
Introduction To Directed Energy Deposition Ded Directed energy deposition (ded) — sometimes just direct energy deposition — is a metal 3d printing technology offering key advantages in larger metal part creation. similar to other metal 3d printing methods, ded builds parts by sintering metal in layers to form a three dimensional structure. There are many pros and cons to each of these solutions. to highlight a few: vacuum – this provides the highest quality environment but requires a heavy, expensive, reinforced chamber to withstand vacuum forces (see system pictured above). Directed energy deposition – pros and cons. ded technology has been there for a long, helping users create and repair components within various niches. so, here are some of the advantages and the limitations the technology offers. pros. helps in repairing components. Ded has several unique advantages compared to other am processes, such as site specific deposition and repair, alloy design, and three dimensional printing of complex shapes.
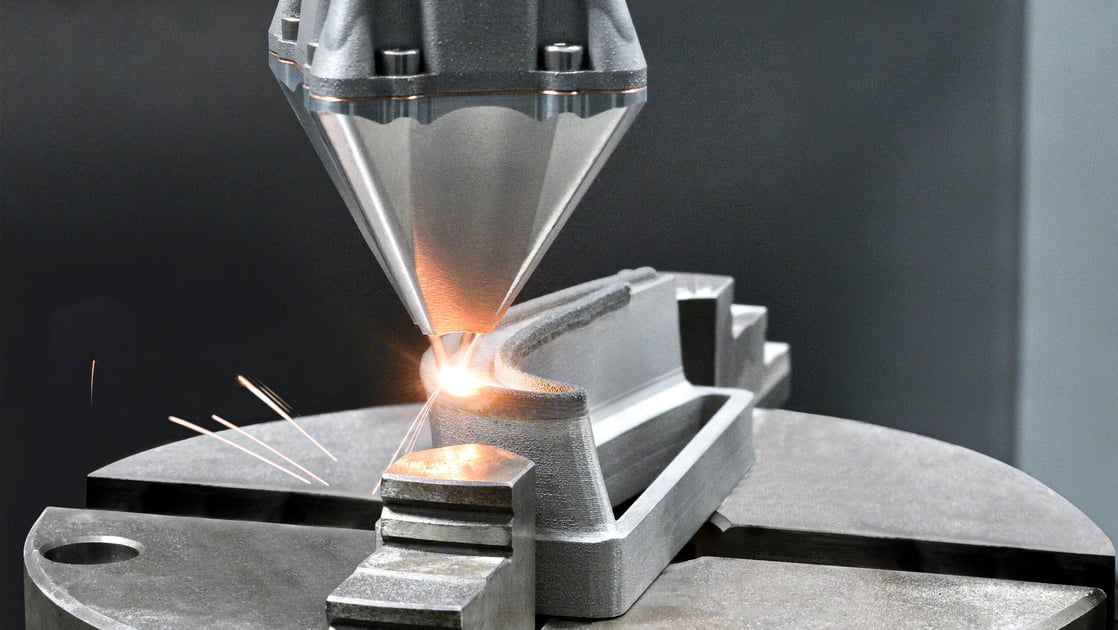
Directed Energy Deposition Ded Metal 3d Printing The Ultimate Guide Directed energy deposition – pros and cons. ded technology has been there for a long, helping users create and repair components within various niches. so, here are some of the advantages and the limitations the technology offers. pros. helps in repairing components. Ded has several unique advantages compared to other am processes, such as site specific deposition and repair, alloy design, and three dimensional printing of complex shapes. While laser powder bed fusion (lpbf) is better for small to medium sized components with high detail and internal features, laser directed energy deposition (lded) combines a material feed system to place the powder onto the exact spot where the laser will melt the material. Direct energy deposition (ded) is a series of several similar metal 3d printing technologies that creates parts by melting and fusing material as it is deposited. while it can be used to manufacture new parts, ded is typically used for repairing and rebuilding damaged components. Direct energy deposition (ded) processes are versatile and powerful additive manufacturing methods due to their rapid deposition, versatility of materials and large scale production capacity. the ded process can produce exceptionally large structures, making it an ideal choice for applications that require scalability and robustness. Advantages and disadvantages of directed energy deposition. being deposited using focused thermal energy such as laser, electron beam or plasma arc. both the energy source. and the material feed nozzle are manipulated using a gantry system or robotic arm. ded is increasingly used in.
Directed Energy Deposition Ded Download Scientific Diagram While laser powder bed fusion (lpbf) is better for small to medium sized components with high detail and internal features, laser directed energy deposition (lded) combines a material feed system to place the powder onto the exact spot where the laser will melt the material. Direct energy deposition (ded) is a series of several similar metal 3d printing technologies that creates parts by melting and fusing material as it is deposited. while it can be used to manufacture new parts, ded is typically used for repairing and rebuilding damaged components. Direct energy deposition (ded) processes are versatile and powerful additive manufacturing methods due to their rapid deposition, versatility of materials and large scale production capacity. the ded process can produce exceptionally large structures, making it an ideal choice for applications that require scalability and robustness. Advantages and disadvantages of directed energy deposition. being deposited using focused thermal energy such as laser, electron beam or plasma arc. both the energy source. and the material feed nozzle are manipulated using a gantry system or robotic arm. ded is increasingly used in.

Schematic Representation Of The Directed Energy Deposition Ded Direct energy deposition (ded) processes are versatile and powerful additive manufacturing methods due to their rapid deposition, versatility of materials and large scale production capacity. the ded process can produce exceptionally large structures, making it an ideal choice for applications that require scalability and robustness. Advantages and disadvantages of directed energy deposition. being deposited using focused thermal energy such as laser, electron beam or plasma arc. both the energy source. and the material feed nozzle are manipulated using a gantry system or robotic arm. ded is increasingly used in.

Directed Energy Deposition Technology Rpm Innovations Rpm Innovations
Comments are closed.